When the fiberglass grating board is just out of the furnace, its appearance does not have a lubricated and clean luster, and it needs to be processed to achieve the expected effect.
The quality of the fiberglass formed parts used in the production of fiberglass grating machines has a significant impact on the appearance of the products and is also closely related to the degree of lubrication. In addition to the quality of these materials, what is important is the overall skill nature of the mold’s quality and service life. However, domestically produced fiberglass molds are a good structure, but compared to other industrialized countries, the appearance quality of the products is poor, as well as the lack of mold materials, manufacturing equipment and conditions. More importantly, most domestic manufacturers do not attach great importance to these details as some foreign factories do, and mainly rely on experience in precision machining of the mold surface.
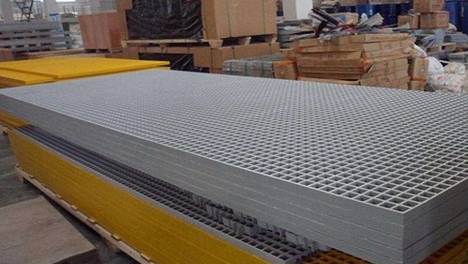
The appearance processing technology of fiberglass molds is introduced as follows:
1. Water grinding method – innovation of new or old modes, water sandpaper is used for water grinding. Water sandpaper is used at the starting point of water grinding, usually from 600. Some users, in order to improve work efficiency, use thicker water sandpaper to directly grind from 400 to 400, quickly grinding. But I don’t know if the failure to polish the coarse sandpaper marks after sanding with fine sandpaper requires re polishing. Then 600 to 800, 1000, 1200, 1500 (or 2000) people lost, and all their efforts were in vain.
2. When polishing, first polish the top surface of the mold, then use an electric polishing machine to polish it, and then apply a rough coating to polish the surface of the mold. When the polishing machine starts the circular spiral operation, do not discharge the cast iron from the mold. The main task is rough polishing. So far, generally speaking, rough polishing requires at least two molds to be completed relatively smoothly. Then rough polish the coarse fibers of the new plate, add fine polishing and polishing agent, and repeat the above operation. The thickness of the polishing agent is different from that of the rough plate, and try to correspond to one for each polishing machine.
3. Clean the mold. During the mold cleaning process, residual oil and release agent in the polishing sealant can firmly adhere to the mold. Then, use Biquan and the mold to scrub twice. For the second mold cleaning, use gauze to scrub the mold surface, dry it, and apply mold cleaning water to allow it to evaporate and dry completely (about half an hour). Finally, use a clean dry lamp.
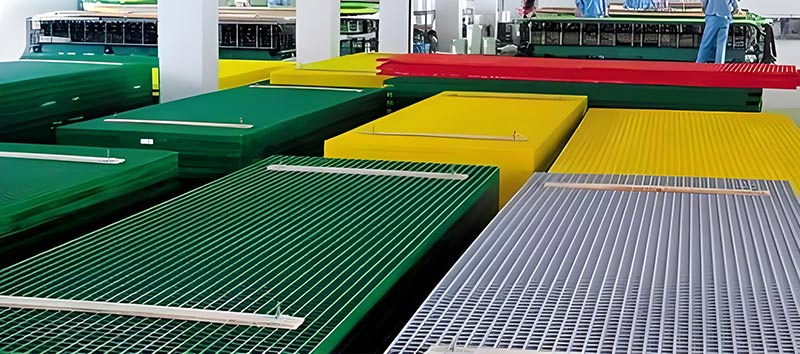
4. Close the mold, and according to the requirements for completing the fiberglass product, it is usually considered complete after the third polishing. However, if only the surface of the mold is polished, there will be many invisible holes. In the precision requirements of fiberglass, we need to seal these tiny holes, so that the precision of fiberglass can be greatly increased, and the reinforcement of plastic can reach a higher level. Apply sealant evenly on the surface of the mold with gauze, then dry (about 30-60 minutes), and then wipe with a clean dry cloth to lubricate. The new mold has also been sealed four times, but if the old mold is innovated, it can be sealed twice.
5. When demolding, different production should be carried out according to different thicknesses of fiberglass products, and different demolding agents should also be selected during the operation. Casting molded fiberglass sanitary ware, with a fiberglass product thickness of about 5 millimeters, and glass curing heating instead of using high-temperature demolding wax or substrate thickness. Try to apply concrete stripping wax with gauze, with an appropriate amount of stripping wax tightly attached to the film. Then squeeze the gauze evenly and apply it to the outside of the mold. This not only ensures uniformity but also saves a lot of scattered un stripped wax, allowing it to dry (30-60 minutes). Then clean the gauze bag by hand and wipe or polish it with a polishing machine to shine. Apply 4-5 times the amount of new release wax before use. After the first 10 products are demolded, the last wax after each demolding can be removed.
In order to improve the completion speed, work efficiency, and demolding performance of fiberglass grating panels, once coated with demoulding agent, the flatness of such products is very good, and it can also avoid the repeated use of demoulding wax for cleaning due to wax fouling. Demoulding wax or reusable clean demoulding wax is prone to oxidation after long-term storage, causing unnecessary damage to fiberglass products. The above is the complete content of the surface treatment process for producing fiberglass grating panels.
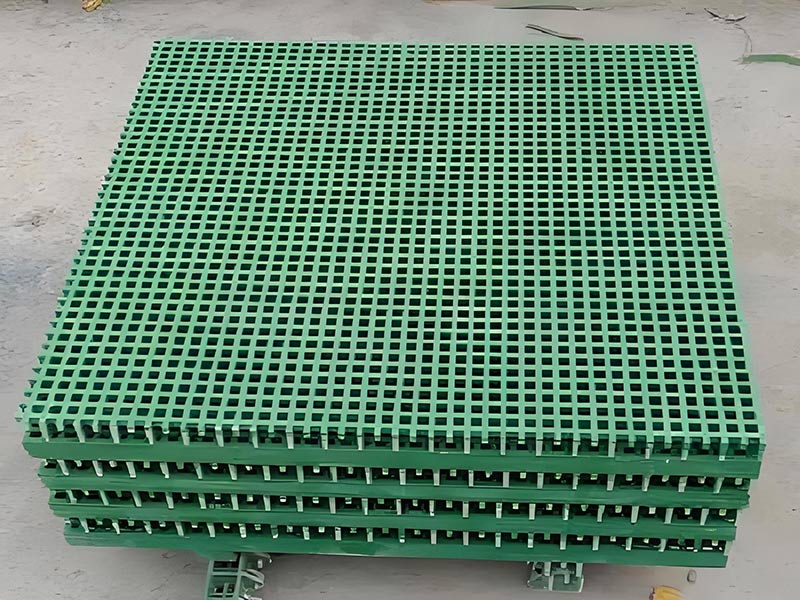