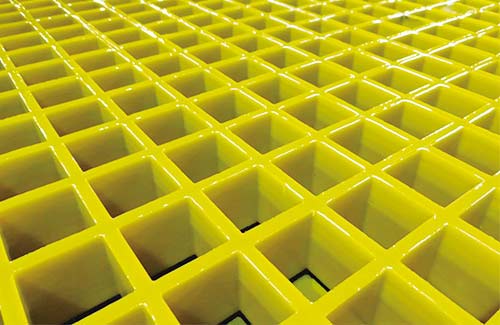
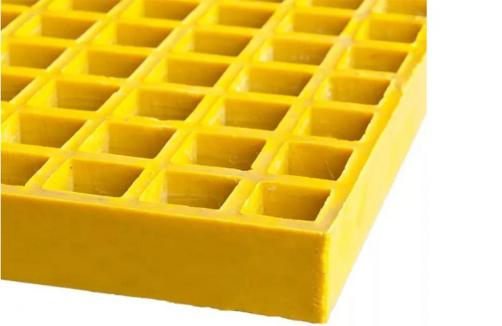
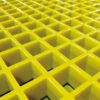
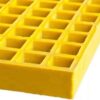
description
Sino Composite offers customer with Molded FRP Grating system. This grating is with advantages of light weight, anti corrosive, high strength and cost efficient. Various of resin, color and specification are available.
Molded FRP(Fiberglass Reinforced Plastic) grating is composed of alternating directional layers of continuous glass fiber for strength, with resin to consolidate the fibers and provide the shape and corrosion-resistance. Due to its bidirectional strength, molded grating can tolerate cutouts in the panel to allow pipe or equipment penetrations without requiring additional support around the opening. Molded grating has very high impact tolerance, as well as the highest chemical resistance of any fiberglass grating. It can be made slip-resistant by adding grit to the surface.
Sino Composite offers customers with both standard and customized panels. We have more than 100 types of standard panels moulds, which could meet almost all the market’s demand.
Sino Composite also offers customers with required molded gratings. Our engineer team will provide with free and professional support.
Sino Composite molded grating includes:
- Square mesh FRP molded grating
- Rectangular mesh FRP molded grating
- Heavy duty square & rectangular FRP molded grating
- Mini&Micro mesh FRP molded grating
- Food grade FRP molded grating
- Conductive FRP molded grating
- Transparent FRP grating
Sino Composite manufactures FRP gratings are available in various of slip resistant surfaces.
FRP molded grating available surface options:
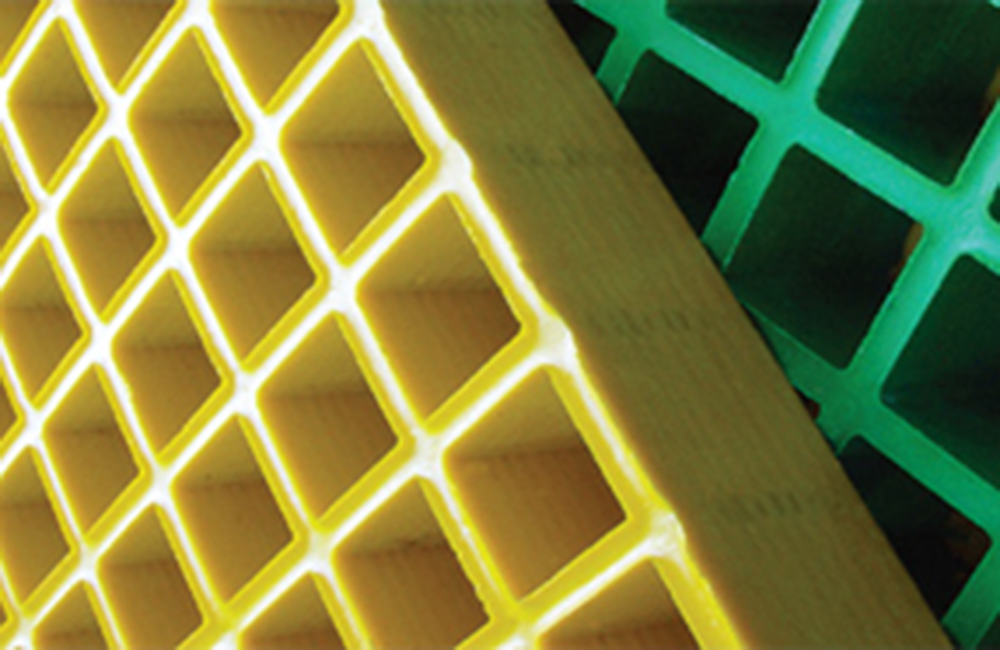
Meniscus or Concave surface
Meniscus surface is widely used surface option. This shape is formed naturally shaped in the mold. It is with good anti slip property and could be process to other surface options.
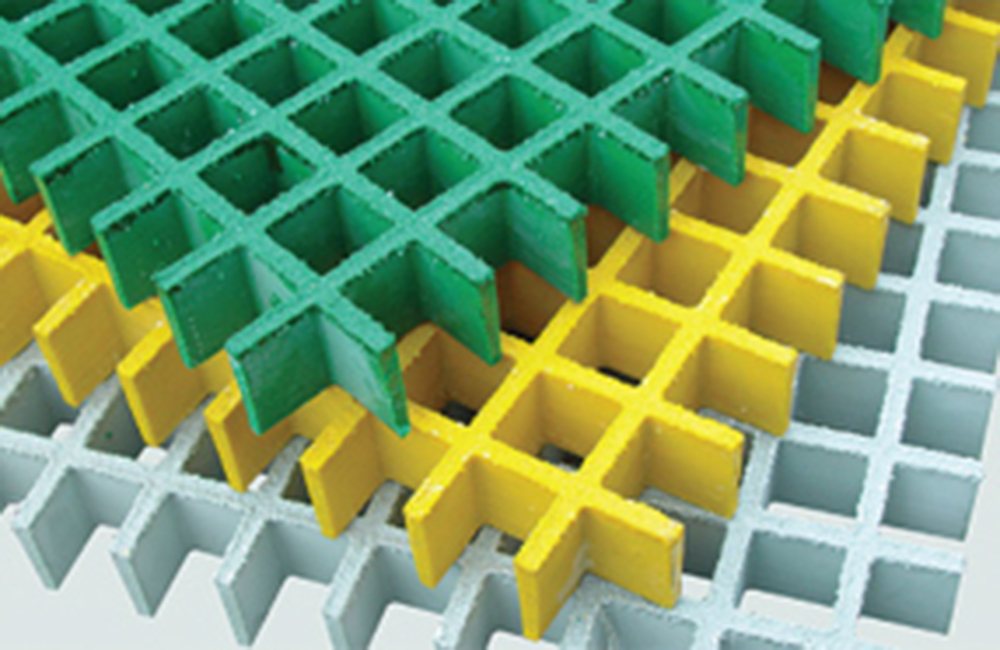
Sand grit surface
It is widely applied in industrial areas. With excellent property of anti slip, it will not impact the strength of grating itself.
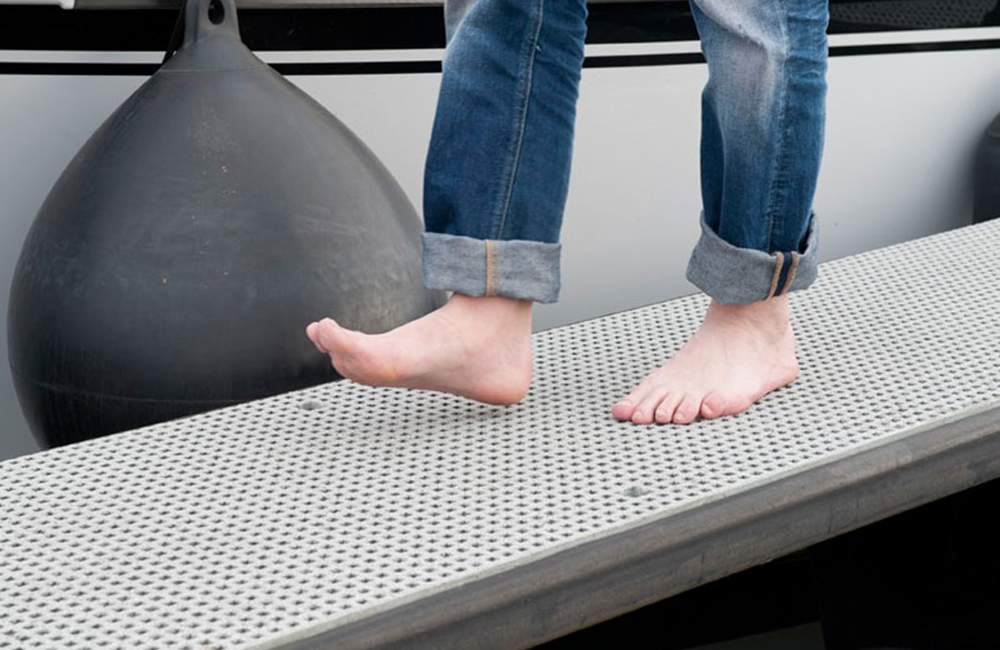
Barefoot grit
Amusement parks, water worlds, and seashores require gratings suitable for barefoot walking. Sino Composite unique surface sanding treatment is perfect for barefoot walking. At the same time, it has strong anti slip ability.
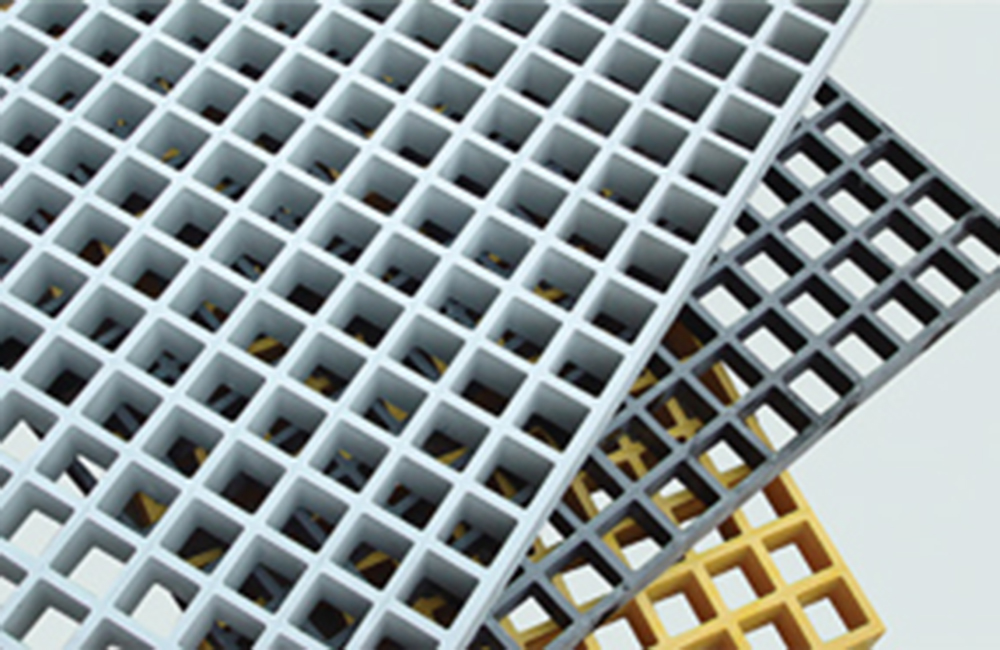
Plain surface
Plain surface is mainly used in architectural features: Curtain walls, fence, etc.
Partially standard FRP molded grating specifications and sizes.
Serial Number | Height(mm) | Mesh size(mm) | Panel Size(mm) | Open Area |
1 | 13 | 38×38 | 1220×3660 | 78% |
2 | 15 | 38×38 | 1220×3660 | 78% |
3 | 20 | 38×38 | 1220×3660 | 65% |
4 | 25 | 38×38 | 1220×3660 | 68% |
5 | 30 | 38×38 | 1220×3660 | 68% |
6 | 35 | 38×38 | 1220×3660 | 56% |
7 | 38 | 38×38 | 1220×3660 | 68% |
8 | 50 | 38×38 | 1220×3660 | 56% |
9 | 60 | 38×38 | 1220×3660 | 56% |
10 | 25 | 40×40 | 1007×4047 | 67% |
11 | 30 | 40×40 | 1247×4047 | 67% |
12 | 40 | 40×40 | 1247×4047 | 67% |
13 | 13 | 50×50 | 1220×4000 | 82% |
14 | 13 | 50.8×50.8 | 1220×4000 | 82% |
15 | 25 | 50×50 | 1220×3660 | 78% |
16 | 40 | 50×50 | 1220×3660 | 80% |
17 | 50 | 50×50 | 1220×3660 | 78% |
18 | 63 | 50×50 | 1220×3660 | 78% |
19 | 25 | 83×83 | 1007×4047 | 84% |
20 | 40 | 83×83 | 1007×4047 | 84% |
21 | 30 | 12.7×12.7/40×40 | 1220×3660 | 30% |
22 | 25 | 19×19/38×38 | 1220×3660 | 40% |
23 | 38 | 19×19/38×38 | 1220×3660 | 40% |
24 | 14 | 20×20/40×40 | 1247×4047 | 42% |
25 | 30 | 20×20/40×40 | 1007×4047 | 42% |
26 | 40 | 20×20/40×40 | 1007×4047 | 42% |
27 | 50 | 25×25/50×50 | 1524×4000 | 55% |
28 | 38 | 26×26/52×52 | 1220×3660 | 60% |
29 | 38 | 25×50 | 1220×3660 | 48% |
30 | 50 | 25×50 | 1220×3660 | 48% |
31 | 25 | 25×100 | 1007×3007 | 67% |
32 | 30 | 25×100 | 1007×3007 | 67% |
33 | 38 | 25×100 | 1220×3660 | 62% |
34 | 38 | 38×100 | 1220×3660 | 65% |
35 | 38 | 25×152 | 1220×3660 | 63% |
36 | 38 | 38×152 | 1220×3660 | 67% |
37 | 50 | 38×100 | 1220×3660 | 62% |
Sino Composite uses different resins to achieve different environments. Covering all resin application ranges, our professional sales team will recommend different resin substrates according to customer needs.
Resin System
Resin Type | Resin Base | Description | Corrosion Resistance | Flame Spread Rating ASTM E84 | Available colors | Max. Oper. Temp. |
Type VEFR-20 | Vinyl Ester | Superior Corrosion Resistance and Fire Retardant | Excellent | Class 1, 20 or less | Dark Gray, Orange | 230℉ |
Type IFR-25 | Isophthalic Polyester | Industrial Grade Corrosion Resistance and Fire Retardant | Very Good | Class 1, 25 or less | Dark Gray, Green | 221℉ |
Type FG-20 | Isophthalic Polyester | Food Grade Corrosion Resistance and Fire Retardant | Very Good | Class 1, 20 or less | Light Gray, Light Green | 221℉ |
Type CFR-25 | Orthophthalic Polyester | Moderate Corrosion Resistance and Fire Retardant | Moderate | Class 1, 25 or less | Green Yellow Light Gray Dark Gray | 212℉ |
Type MP-4 | Phenolic | Low Smoke and Superior Fire Resistance | Very Good | Class 1, 5 or less | Reddish-Brown | 356℉ |
Type IFR-10 | Isophthalic Polyester | Industrial Grade Corrosion Resistance and Extra Fire Retardant | Very Good | Class 1, 10 or less | Custom | 221℉ |
During nearly 20 years of FRP grating production time, our products are widely used in various industries. Petroleum industry, chemical industry, municipal construction, marine engineering, solar energy, architectural decoration, etc.
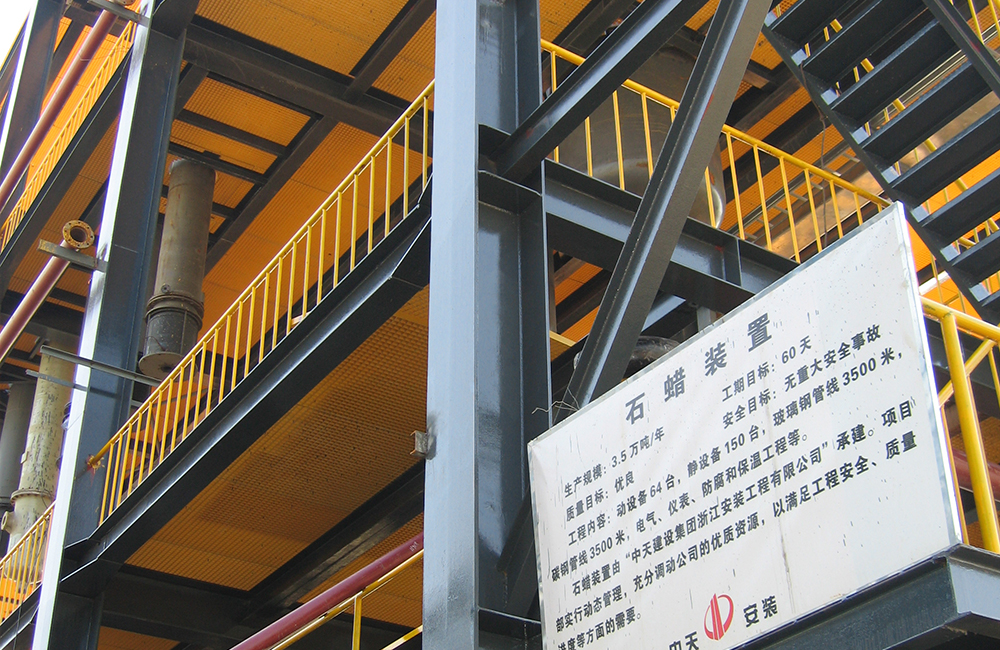
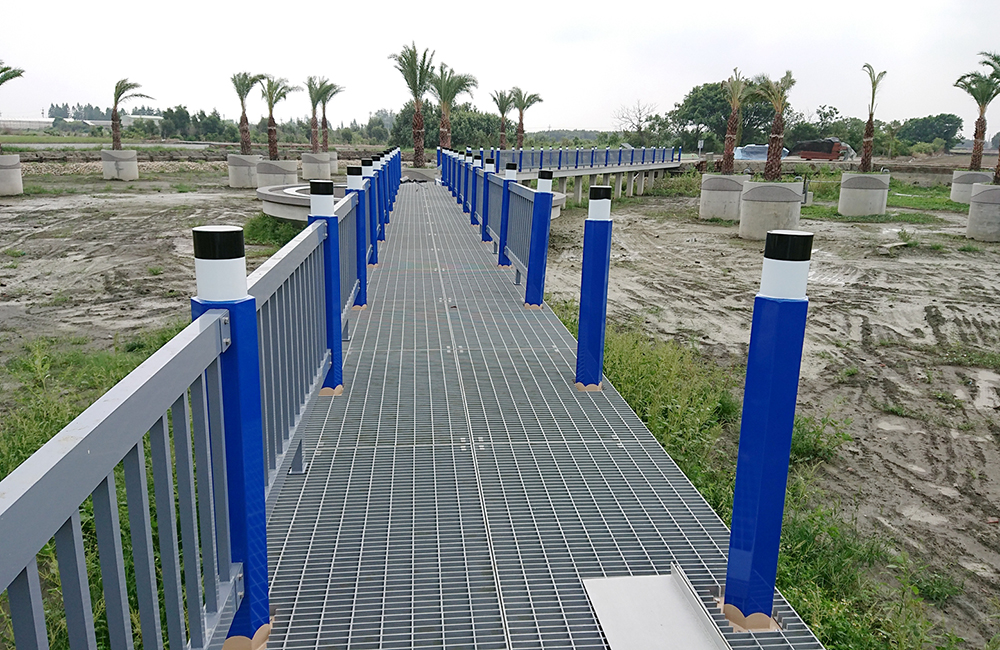
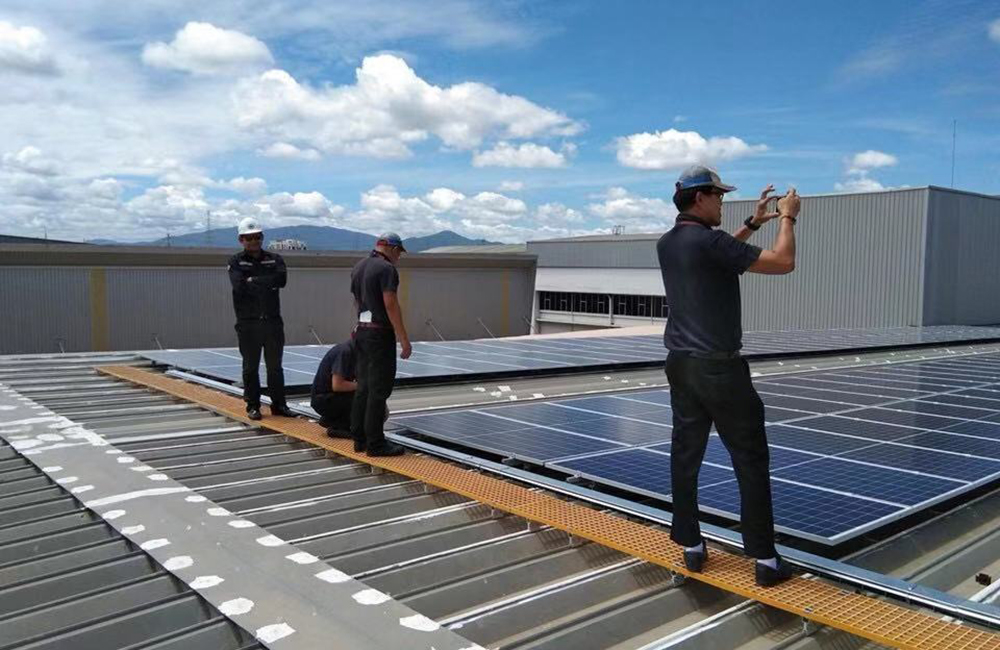
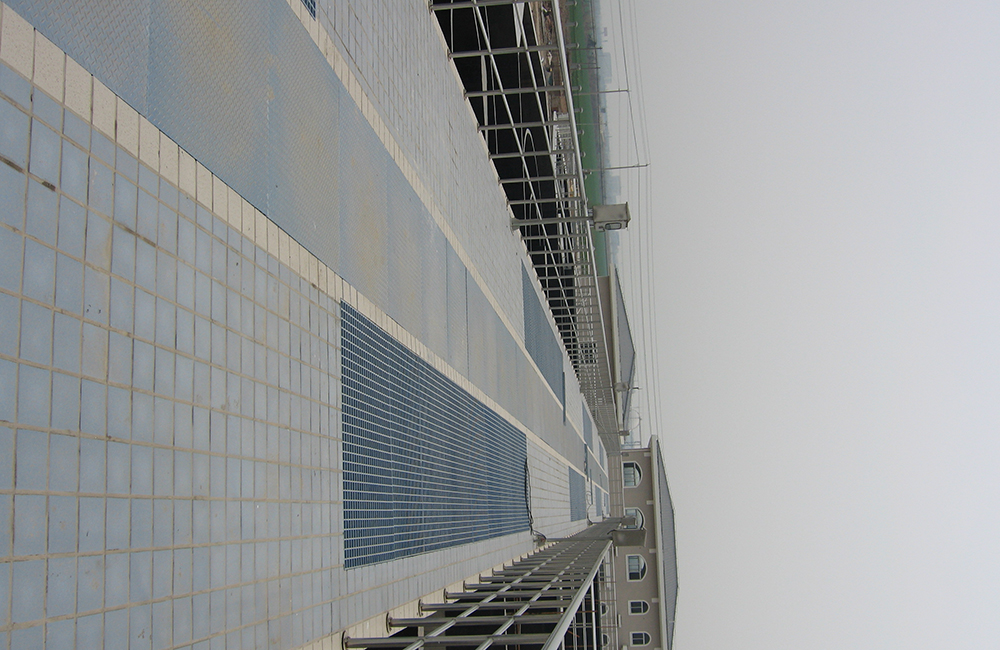
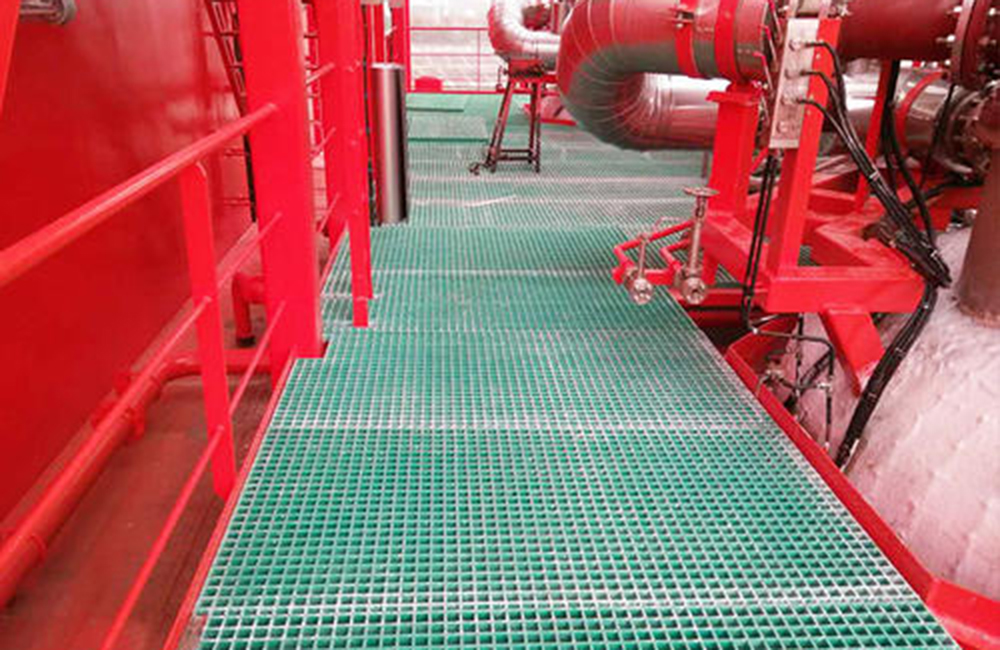
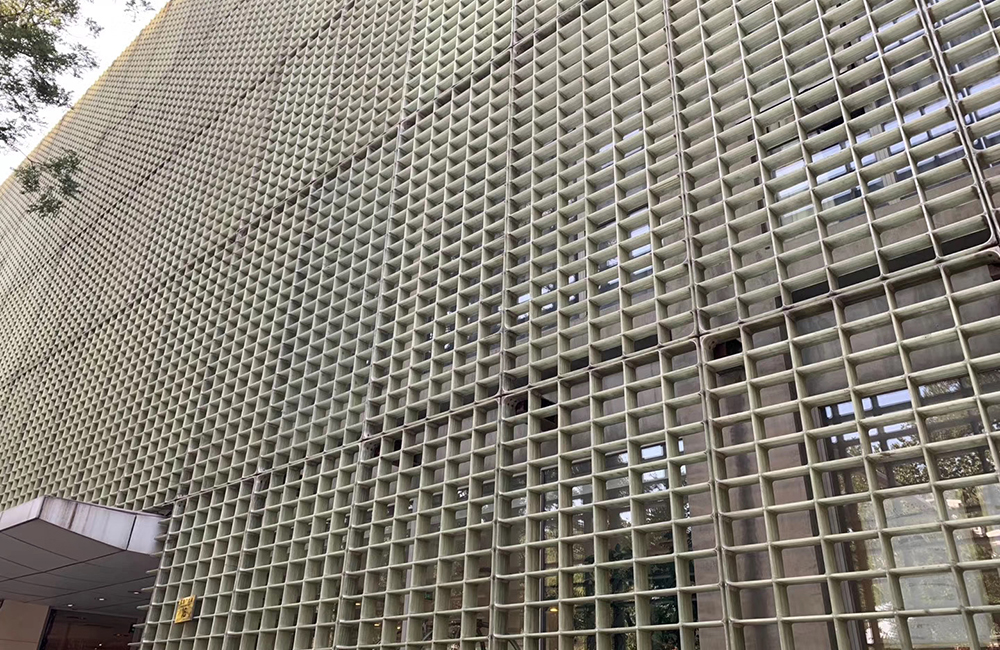
Introduction to FRP Molded Grating
Fiber Reinforced Plastic (FRP) molded grating is a composite material that has become a cornerstone in the construction and industrial sectors, offering a unique blend of strength, durability, and corrosion resistance. This material is made by combining high-strength glass fibers with thermosetting resins, such as unsaturated polyester, vinyl ester, or phenolic resins, and then molding them under heat and pressure to form a robust, one-piece structure. The resulting product is a lightweight, high-strength, and chemically resistant solution for walkways, platforms, stair treads, and other structural components. FRP molded grating is particularly well-suited for environments where traditional materials like steel, aluminum, and wood are prone to degradation due to exposure to harsh chemicals, moisture, or extreme temperatures.
Composition and Manufacturing Process
Materials
– Glass Fibers: These provide the primary reinforcement, contributing to the tensile strength and overall rigidity of the grating.
– Thermosetting Resins: These act as the matrix, binding the fibers together and providing the grating with its shape and chemical resistance. Common resins include:
– Unsaturated Polyester Resin (UPR): Widely used due to its cost-effectiveness and good mechanical properties.
– Vinyl Ester Resin (VER): Offers superior chemical resistance and is often used in more demanding applications.
– Phenolic Resin: Known for its excellent fire resistance and thermal stability, making it suitable for high-temperature environments.
– Fillers and Additives: These can include pigments for color, fire retardants, UV stabilizers, and anti-static agents, which enhance the performance and appearance of the final product.
Manufacturing Process
The manufacturing process for FRP molded grating is a carefully controlled operation that ensures the quality and consistency of the final product. Here’s an overview of the key steps:
1. Preparation of Molds:
– High-precision molds are prepared, designed to create the bi-directional grid pattern characteristic of the grating.
– The mold design includes features such as ribs, crossbars, and surface textures, which are critical for the grating’s performance and safety.
2. Resin Impregnation:
– Glass fibers are impregnated with the chosen resin, ensuring that each fiber is fully coated.
– The impregnation process can be done using various techniques, such as spray-up, hand lay-up, or pultrusion, depending on the specific requirements and production scale.
3. Molding:
– The resin-impregnated fibers are placed into the mold, which is then closed and subjected to heat and pressure.
– The compression molding process ensures that the fibers and resin are uniformly distributed and bonded, creating a solid, one-piece structure.
– The temperature and pressure are carefully controlled to achieve optimal curing and to ensure that the grating meets the required specifications.
4. Curing:
– The heat and pressure cause the resin to cure, transforming it from a liquid to a solid state.
– The curing process is critical, as it determines the final properties of the grating, including its strength, rigidity, and chemical resistance.
– Curing times and temperatures vary depending on the type of resin and the desired properties of the grating.
5. Finishing and Quality Control:
– Once cured, the grating is removed from the mold, trimmed, and inspected for quality.
– Additional treatments, such as adding slip-resistant surfaces, can be applied at this stage.
– Quality control measures, including visual inspection, dimensional checks, and load testing, are performed to ensure that the grating meets the required standards.
Key Features and Benefits
Lightweight and High Strength
– Lightweight: FRP molded grating is significantly lighter than metal gratings, making it easier to handle, transport, and install. This reduces labor costs and installation time.
– High Strength: Despite its light weight, FRP grating offers comparable or even superior load-bearing capacity, thanks to the high tensile strength of the glass fibers.
– Strength-to-Weight Ratio: The combination of high strength and low weight results in an excellent strength-to-weight ratio, which is crucial for applications where both factors are important.
Corrosion Resistance
– Chemical Resistance: FRP molded grating is highly resistant to a wide range of corrosive substances, including acids, alkalis, and solvents. This makes it ideal for use in chemical processing plants, wastewater treatment facilities, and marine environments.
– Longevity: The corrosion resistance of FRP ensures that the grating remains structurally sound and aesthetically pleasing over a long period, reducing the need for frequent replacement.
Non-Conductive
– Electrical Insulation: FRP is an excellent electrical insulator, making it a safe choice for applications where electrical conductivity could pose a risk. This property is particularly valuable in electrical substations, power generation facilities, and other settings where electrical safety is paramount.
– Safety: The non-conductive nature of FRP helps prevent electrical accidents, enhancing the safety of personnel and equipment.
Fire Retardant
– Flame Spread and Smoke Generation: Many FRP formulations are designed to meet stringent fire safety standards, offering low flame spread and smoke generation. This is crucial for ensuring the safety of personnel and structures in the event of a fire.
– Fire Ratings: FRP molded grating can be manufactured to meet various fire ratings, such as ASTM E84, UL 94, and others, depending on the specific application requirements.
Slip-Resistant
– Surface Textures: The surface of FRP molded grating can be treated with various textures to enhance slip resistance, improving safety in wet, oily, or icy conditions. Common surface treatments include:
– Gritted Surface: A fine grit is embedded into the surface, providing excellent traction.
– Concave Surface: Small, concave shapes on the surface help to channel water and debris away, reducing the risk of slips.
– Covered Surface: A smooth, covered surface can be added for a more aesthetic finish while still maintaining some level of slip resistance.
– Customization: The surface texture can be customized based on the specific needs of the application, ensuring optimal safety and performance.
Low Maintenance
– Durability: Unlike metal gratings, FRP does not require regular painting or coating to prevent rust and corrosion. It is also resistant to rot and decay, reducing the need for frequent maintenance.
– Cost-Effective: The low maintenance requirements of FRP molded grating result in lower long-term costs, as there is no need for frequent repairs or replacements.
– Long Service Life: The durability and resistance to environmental factors contribute to a longer service life, further enhancing the cost-effectiveness of the material.
Customizable
– Color Options: FRP molded grating can be manufactured in a variety of colors, allowing for aesthetic customization and improved visibility. This is particularly useful in environments where color coding or visual distinction is important.
– Size and Shape: The size and shape of the grating can be tailored to fit specific project requirements, ensuring a perfect fit and optimal performance.
– Design Flexibility: The ability to customize the grating allows for greater design flexibility, enabling architects and engineers to create structures that are both functional and visually appealing.
Applications
Industrial Sectors
– Chemical Processing: FRP molded grating is widely used in chemical plants for platforms, walkways, and stair treads, where resistance to corrosive chemicals is essential.
– Water and Wastewater Treatment: In water treatment facilities, FRP grating is used for walkways and platforms, providing a durable and low-maintenance solution in a wet and potentially corrosive environment.
– Oil and Gas: FRP grating is ideal for offshore platforms, refineries, and petrochemical plants, where it can withstand exposure to saltwater, oil, and other harsh chemicals.
– Food and Beverage: In food processing facilities, FRP grating is used for platforms, walkways, and drainage systems, where hygiene and corrosion resistance are critical.
Commercial and Infrastructure
– Marine and Coastal Structures: FRP grating is used in docks, piers, and boat ramps, providing a durable and slip-resistant surface in marine environments.
– Parks and Recreation: In parks and recreational areas, FRP grating is used for boardwalks, observation decks, and outdoor walkways, offering a low-maintenance and aesthetically pleasing solution.
– Transportation: FRP grating is used in bridges, pedestrian overpasses, and train station platforms, providing a strong and durable surface that can withstand heavy foot traffic and environmental exposure.
Installation and Design Considerations
Load Capacity
– Static and Dynamic Loads: When designing with FRP molded grating, it is essential to consider both static and dynamic loads. Static loads include the weight of the structure itself and any permanent fixtures, while dynamic loads include the weight of people, vehicles, and other moving objects.
– Load Tables and Design Guidelines: Manufacturers provide detailed load tables and design guidelines to help engineers and designers select the appropriate grating and support system. These tables typically include information on span, load capacity, and deflection limits.
Support Systems
– Support Spacing: Proper support spacing is crucial for the longevity and performance of FRP molded grating. Supports should be evenly spaced and capable of distributing the load effectively. Common support systems include I-beams, C-channels, and angle iron.
– Support Configuration: The configuration of the support system, including the orientation and spacing of supports, can affect the load-carrying capacity and deflection of the grating. Engineers should consult the manufacturer’s guidelines to ensure proper support design.
Fastening Methods
– Clips and Bolts: FRP grating can be fastened using clips, bolts, and other mechanical fasteners. Clips are commonly used for attaching the grating to the support structure, while bolts can be used for securing the grating in place.
– Adhesives: In some cases, adhesives may be used to bond the grating to the support structure. This method is particularly useful when a seamless, watertight connection is required.
– Edge Treatments: Edge treatments, such as edge trim and corner pieces, can be used to protect the edges of the grating and provide a finished look. These treatments also help to prevent damage and improve safety.
Environmental Factors
– Temperature and Humidity: FRP molded grating is generally resistant to temperature and humidity, but certain additives and coatings can further enhance its performance in challenging environments. For example, UV stabilizers can be added to protect the grating from UV radiation, and fire retardants can be used to improve its fire resistance.
– Exposure to Chemicals: While FRP is highly resistant to many chemicals, it is important to select the appropriate resin and additives based on the specific chemicals present in the environment. For example, vinyl ester resin is often used in environments with high concentrations of acids and alkalis.
– UV Radiation: Prolonged exposure to UV radiation can cause some types of FRP to degrade over time. To mitigate this, UV stabilizers can be added to the resin, and the grating can be coated with a protective layer.
Cost-Effectiveness
– Initial Cost vs. Long-Term Savings: While the initial cost of FRP molded grating may be higher than that of some traditional materials, its long-term cost-effectiveness is often superior. The reduced need for maintenance, longer service life, and lower installation costs can result in significant savings over the lifetime of the grating.
– Maintenance Costs: The low maintenance requirements of FRP grating, including the absence of painting and coating, contribute to lower ongoing costs. Additionally, the durability of the material means that it does not need to be replaced as frequently as other materials, further reducing costs.
– Installation Costs: The lightweight nature of FRP grating makes it easier and faster to install, reducing labor costs and installation time. This can be a significant advantage in large-scale projects where installation efficiency is crucial.
Sustainability
– Environmental Impact: FRP molded grating is an environmentally friendly option, as it is made from non-toxic materials and can be recycled at the end of its useful life. The production process for FRP is also more energy-efficient compared to the production of metals like steel and aluminum.
– Durability and Longevity: The durability and long service life of FRP grating contribute to a smaller overall environmental footprint. By lasting longer and requiring less maintenance, FRP grating reduces the need for frequent replacement and the associated waste.
– Recycling and Disposal: At the end of its useful life, FRP grating can be recycled or repurposed, reducing the amount of waste sent to landfills. Some manufacturers offer recycling programs for their products, further enhancing the sustainability of the material.
Case Studies and Real-World Examples
Chemical Processing Plant
– Challenge: A chemical processing plant needed a durable and corrosion-resistant solution for walkways and platforms in areas exposed to harsh chemicals.
– Solution: FRP molded grating was selected for its excellent chemical resistance and low maintenance requirements. The grating was installed with a gritted surface for enhanced slip resistance.
– Outcome: The FRP grating provided a long-lasting, safe, and cost-effective solution, reducing the need for frequent maintenance and extending the service life of the walkways and platforms.
Water Treatment Facility
– Challenge: A water treatment facility required a durable and slip-resistant solution for walkways and platforms in a wet and potentially corrosive environment.
– Solution: FRP molded grating with a concave surface was chosen for its superior slip resistance and chemical resistance. The grating was installed with a custom support system to ensure proper load distribution.
– Outcome: The FRP grating provided a safe and reliable solution, enhancing the safety of workers and reducing the need for maintenance. The grating’s durability and resistance to environmental factors ensured a long service life.
Offshore Platform
– Challenge: An offshore platform needed a lightweight and corrosion-resistant solution for walkways and platforms in a marine environment.
– Solution: FRP molded grating was selected for its lightweight, high-strength, and corrosion-resistant properties. The grating was installed with a gritted surface and a custom support system to withstand the harsh marine conditions.
– Outcome: The FRP grating provided a durable and low-maintenance solution, reducing the weight and complexity of the platform’s structure. The grating’s resistance to saltwater and other marine elements ensured a long service life and enhanced safety for workers.
Future Trends and Innovations
– Advanced Resins and Additives: Ongoing research and development are focused on developing new resins and additives that can further enhance the properties of FRP molded grating. This includes resins with improved fire resistance, UV stability, and chemical resistance.
– Sustainable Production: There is a growing emphasis on sustainable production methods, including the use of renewable raw materials and more energy-efficient manufacturing processes. This aligns with the increasing demand for environmentally friendly solutions in the construction and industrial sectors.
– Smart and Integrated Solutions: The integration of smart technologies, such as sensors and monitoring systems, into FRP molded grating is a potential future trend. This could enable real-time monitoring of the grating’s condition, enhancing safety and maintenance planning.
– Customization and Modularity: Advances in manufacturing technology are likely to lead to increased customization and modularity, allowing for more tailored solutions that meet specific project requirements. This could include the development of modular systems that can be easily assembled and reconfigured as needed.
Conclusion
FRP molded grating is a versatile, durable, and cost-effective solution for a wide range of industrial and commercial applications. Its combination of strength, corrosion resistance, and low maintenance makes it an attractive alternative to traditional materials. Whether used in harsh industrial environments or in more aesthetically driven projects, FRP molded grating offers a reliable and sustainable option for enhancing safety, efficiency, and performance. As technology continues to advance, the potential applications and benefits of FRP molded grating are likely to expand, making it an increasingly important material in modern construction and engineering.